Статистика

Онлайн всего: 1 Гостей: 1 Пользователей: 0
|
Точність взаємного розташування поверхонь
Точність взаємного розташування циліндричних, конічних, плоских і криволінійних поверхонь має важливе значення для правильного виконання деталями свого призначення в конструкції вузла або машини.
У кресленнях деталей вичерпно чітко і ясно повинні бути внесені необхідні вказівки, що визначають точність взаємного розташування поверхонь відповідно до умов роботи деталей у вузлі. Ці формулювання повинні бути безперечними за своїм змістом з тим, щоб абсолютно виключити неправильні, довільні їх тлумачення.
Вносячи подібні технічні умови в креслення, конструктор об'єкту повинен ясно віддавати собі звіт в реальності і можливості їх виробничого забезпечення і технічного контролю, в можливості побудови необхідних для даного випадку контрольно-вимірювальних засобів (калібрів, контрольних пристосувань і приладів). Це є обов'язковою складовою частиною технологічного аналізу своєї конструкції, який повинен зробити конструктор.
До точності взаємного розташування циліндричних деталей відносяться радіальне биття, відхилення від співісності, коливання відстані між осями, непаралельність, схрещування і неперпендикулярність осей, точність розташування отворів. При технічній необхідності креслення повинне обмежувати відповідні відхилення.
Радіальне биття - різниця відстаней від циліндричної поверхні, що перевіряється, до осі деталі.
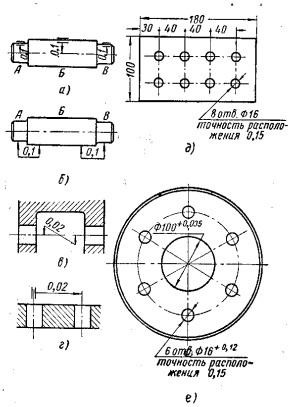
Фіг.2
Вісь деталі може визначатися віссю центрових отворів (фіг. 2, а) або інший -базовою циліндричною поверхнею, яка повинна бути співвісна з тією, що перевіряється (фіг. 2, би).
У першому випадку радіальне биття поверхонь А, Б і В повинно бути виміряне відносно осі центрових отворів деталі. У другому випадку . радіальне биття поверхонь А і В повинно бути перевірено при установці деталі по поверхні б.
Вибір між двома приведеними методами обмеження радіального биття повинен бути зроблений конструктором об'єкту залежно від вимог до самої деталі і реальної можливості її контролю.
При вимірюванні по першій схемі найбільше радіальне биття поверхонь А, Б і В можуть виявитися направленими в різні боки і сума їх може вийти більшою, ніж це припускав конструктор. Разом з тим вимірювання радіального биття валів відносно
осі їх центрових отворів, як правило, найбільш легке здійснюється у виробничих умовах.
При другій схемі вимірювання радіального биття поверхонь А і В необхідно виявляти відносно базової поверхні деталі Б, що правильніше, оскільки відповідає умовам роботи деталі у вузлі. Проте при даній схемі часто не можна обмежуватися універсальними контрольно-вимірювальними засобами і доводиться передбачати спеціальні, контрольні пристосування. Враховуючи важливість обмеження радіального биття для роботи вузла, а також допустиму величину цього биття, конфігурацію деталі і можливість її контролю без використання центрових отворів, в кресленні деталі повинно бути, вписана відповідна технічна умова в найдоцільнішому для даного випадку формулюванні.
У радіальне биття, окрім відхилення від співісності циліндричних поверхонь,
включає похибку геометричної форми (овальність, огранку, конусність і ін.). Виділити відхилення геометричної форми при контролі радіального биття важко і практично недоцільно. Цю обставину повинен враховувати конструктор об'єкту при встановлення меж допустимих відхилень по радіальному биттю.
Відхилення від співісності визначається відносним паралельним зсувом осей, а також їх перекосом. Таким чином, відхилення від співісності циліндричних поверхонь відповідає взаємному зсуву осей, тоді як радіальне биття передбачає подібне ж відхилення циліндричних поверхонь, що перевіряються, але в подвоєному розмірі (подвійний ексцентриситет осей). Відхилення в співвісності рознесених коротких циліндричних поверхонь (фіг. 2; в), як правило, важко виміряти. Це пояснюється погрішностями установки вимірника в отворі при несприятливому співвідношенні його діаметру і довжини, тобто коли розмір діаметру більше довжини отвору.
Разом з тим у великій кількості випадків немає необхідності вимірювати дійсні величини відхилень від співвісності, достатнім є контроль за правильним монтажним сполученням відповідних деталей.
Непаралельність осей (фіг. 2, г) - різниця відстані між осями, розташованими в загальній площині, і віднесена до відстані між двома точками, по яких здійснюється вимірювання. У кресленні може задаватися довжина, на якій встановлений допуск на непаралельність осей (наприклад, «непаралельність осей отворів D1 і D2 допускається в межах 0,05 на довжині 100 мм»).
У випадках, коли довжина, на якій задано відхилення по непаралельності осей, не обумовлена кресленням, передбачається, що допуск на непаралельність відноситься до всієї довжини поверхні, що перевіряється.
Схрещування осей - відхилення від знаходження в загальній площині двох паралельних осей. Схрещування осей є частковим елементом їх непаралельності і не обов’язково повинно вказуватися в кресленні, якщо його відхилення не відрізняється по величині від допустимого відхилення в паралелі осей, розташованих в загальній площині.
Можливий випадок одночасної непаралельності і схрещування осей. При цьому виявляється розташування однієї осі відносно іншої під деяким кутом і до вимірювання увійде деяка похибка.
Неперпендикулярність осей - відхилення від прямого кута між двома осями, виражене в граничному лінійному або кутовому відхиленні на заданій довжині. Розташування осей під кутом, відмінним від прямого, обмежує відхилення від заданого кута.
Точність розташування отворів визначається радіусом розсіювання центру кожного отвору від центру, побудованого за номінальними розмірами.
У прикладі на фіг. 2, д приведений випадок, коли центр кожного з восьми отворів діаметром 16 мм може відхилятися в будь-яку сторону в межах радіусу, рівного 0,15 мм.
У випадку, якщо деталь має базову поверхню, щодо якої (а не тільки між собою) повинні бути правильно розташовані отвори, що перевіряються, ця поверхня повинна бути прийнята за базу вимірювання, навіть якщо це і не вказано в кресленні деталі. Так, в прикладі на фіг. 2, е деталь повинна бути при вимірюванні встановлена по отвору діаметром 100+0.35 мм для перевірки точності розташування отворів діаметром 16+0.2 мм як між собою, так і щодо базового отвору діаметром 100 +0.035 мм.
Конструктор об'єкту повинен враховувати, що при контролі точності розташування отворів виконавчі розміри відповідних калібрів і контрольних пристосувань розраховуються, виходячи з якнайменших розмірів отворів, що перевіряються і базових, тобто без урахування допустимих відхилень на їх діаметри. При інших (в межах допусків на діаметри) розмірах отворів деталі відхилення від заданої точності їх розташування може виявитися великим, що відповідає контролю за принципом забезпечення складання вузла.
Взаємне розташування плоских поверхонь визначається відхиленнями від паралельності, перпендикулярності і розташування під кутом, відмінним від 90°. Допуски на ці відхилення в кресленнях можуть відноситися до заданої довжини (наприклад, непаралельність поверхонь П і П1, допускається в межах 0,1 на довжині 100 мм) або до всієї довжини поверхні, що перевіряється (наприклад, непаралельність поверхонь П і П1 допускається в межах 0,1 мм).
Часто зустрічається необхідність обмеження неточності взаємного розташування циліндричних і плоских поверхонь, як, наприклад: торцеве биття, відхилення від паралельності (або перпендикулярності) плоских і циліндричних поверхонь, комбіноване биття.
Торцеве биття (фіг. 3, а) - різниця виміряних паралельно осі відстаней торцевої поверхні деталі від площини, перпендикулярної до осі. У кресленні можна вказувати довжину (радіус або діаметр), щодо якої задається допуск па торцеве биття. Якщо ця довжина не вказується, то передбачається, що допуск на торцеве биття відноситься до всієї поверхні, що перевіряється.
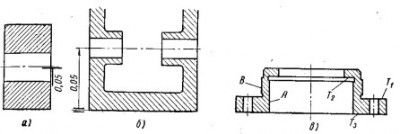
Фіг.3
Непаралельність (фіг. 3, 6) циліндричних поверхонь плоским аналогічна непаралельності циліндричних поверхонь, циліндричних або плоских поверхонь плоским. Те ж відноситься і до неперпендикулярності.
Биття при комбінованому базуванні відповідає випадкам, коли деталі базуються у вузлі не по одній поверхні, а комбінований - центрування деталі відбувається по циліндричній поверхні з одночасною опорою по площини.
Наприклад, для стакана підшипників (фіг. 3, в) технічна умова прийме, наприклад, наступний вигляд:
«При установці по поверхні В і опорі на торець Т1 допускається:
а) биття поверхні А в межах 0,02 мм;
б) биття торця Т2 в межах 0,03 мм;
в) биття торця Т3 в межах 0,05 мм.
|
Календар
« Травень 2024 » | Пн | Вт | Ср | Чт | Пт | Сб | Нд | | | 1 | 2 | 3 | 4 | 5 | 6 | 7 | 8 | 9 | 10 | 11 | 12 | 13 | 14 | 15 | 16 | 17 | 18 | 19 | 20 | 21 | 22 | 23 | 24 | 25 | 26 | 27 | 28 | 29 | 30 | 31 |
|